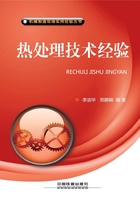
6.如何清除工件表面附着的残油?
热处理前,经常会发现一些工件表面附着一些残油或固体污染物,这些残油或污染物如果处理不好使之进入炉内加热挥发或燃烧,会造成车间空气污染甚至影响热处理质量。对工件表面附着残油或固体污染物的清洗方法主要有碱水清洗法、金属清洗剂清洗方法、有机溶剂清洗方法、燃烧脱脂法和高级清洗技术。
(1)碱水清洗法
最简单的碱水清洗是直接加热或间接加热式的清洗槽,清洗液是(3%~10%)的N2CO3或NaOH水溶液。
渗碳(碳氮共渗)工件,回火前的中间清洗多用加热到70~80℃的5%~10%浓度的碳酸钠溶液。密封箱式多用炉和连续式渗碳炉生产线上的中间清洗机即属于此类。工件碱液清洗可采取喷淋和浸入双重方式,然后用热清水冲洗。最后利用工件的自身余热进行干燥。碱水清洗方法最主要缺点是清洗效果不太好,尤其工件的盲孔和凹部易有污斑和残留物。
(2)金属清洗剂清洗方法
为克服碱水清洗方法的缺点,提高清洗效果,目前可采用专用金属清洗剂,将清洗剂在40~80℃的水中稀释成(1%~3%)溶液,将工件在溶液中浸泡15~20min,然后用热水漂洗,最后用脱水油进行脱水处理。可加入清洗机中使用。
金属清洗剂清洗方法缺点是价格贵,并有难闻的气味,对工件有腐蚀作用,且产生的废水会污染环境,因此必须对废水进行处理,并回收废油。
(3)有机溶剂清洗方法
使用三氯乙烷、三氯乙烯等有机溶剂清洗,清洗效果佳。但在常压下以浸泡或喷淋方式清洗淬火工件时,有机溶剂的挥发和飞溅会污染环境。为此,可采用密闭减压溶剂真空清洗法的全套装置,利用真空泵把空气排出,工件在没有空气情况下和高密度的溶剂蒸汽均匀接触,进一步提高清洗效果,并靠真空蒸馏回收溶剂和油。回收后的油中溶剂含量由20%降至4%以下,清洗结束,打开清洗机密封盖时,溶剂蒸汽浓度在10ppm以下,低于三氯乙烯环境卫生规定的50ppm。
(4)燃烧脱脂法
机加工件在进入热处理工序之前,需要清洗掉表面的油类。为此,可把工件在脱脂炉内加热至450~500℃使油份汽化或燃烧,以达到工件去油的目的。
燃烧脱脂法仅适用于热处理前的清洗,也能清洗切削油、防锈油等轻质、低黏度及低沸点油类。像高黏度、高沸点的重质淬火油燃烧后会有大量残留物和炭黑附着在工件表面,达不到清洗目的。
(5)高级清洗技术
对于采用低压真空渗碳等工艺处理的汽车零件(如汽车发动机零件、商用车变速器同步环套、轿车变速器零件)及航空发动机零件等,需要采用高级环保清洗工艺和设备,如采用真空清洗工艺及设备、超声波清洗工艺及设备等。零件清洗后,不仅对环境无污染,还可以达到很高的清洁度,满足了环保和对零件高清洁度的要求。高级清洗技术主要包括高级清洗技术、真空水基清洗技术、超声波清洗技术等。
真空溶剂清洗技术。真空溶剂清洗由于采用碳氢化合物溶剂作为清洗剂,对淬火油、切削液及防锈液等具有很强的溶解能力,采用真空溶剂清洗机(如VCH系列)在真空状态下,对工件进行预洗喷淋、蒸汽喷淋、循环喷淋及真空干燥等清洗流程,具有高效、稳定的清洗能力和极佳的清洗效果,更加节能环保,设备安全性好,生产效率高。特别适合于真空及渗氮热处理等对于高端清洗要求的零件。
真空清洗工艺流程为:装入工件(约1min)→抽真空(约3min)→预洗喷淋(约1min)→快速蒸汽清洗(约8min)→循环喷淋(约5min)→真空干燥(约7min)→取出工件(约2min),整个过程约35min。
从清洗效果看,通过在真空状态下使用碳氢化合物溶剂和溶剂蒸汽对工件进行有效清洗,然后真空负压干燥工件。同时再生装置在真空负压状态下对溶剂进行蒸馏,并冷凝回收纯净溶剂。分离出的废液收集后单独排除,不但可以获得优质的清洗效果,而且环保。
真空水基清洗技术。水系真空清洗是利用淬火油等挥发性液体减压后沸点下降,和油、水、水蒸汽等一起加热,其沸点也下降的原理进行清洗。由于是(真空)减压清洗,对杯状或盲孔状零件清洗效果好,并能够实施真空干燥(脱脂),而且清洗温度较高,对渗碳淬火后需进行低温回火的零件可实现清洗、回火一并完成。省略了回火工序,节省了能源,达到了节能和环保的要求,属于清洁环保的清洗技术。
清洗过程如采用VCE系列真空水基清洗机进行清洗,其清洗过程主要有前清洗、真空清洗及真空干燥。
前清洗。工件被送往前室后,采用微喷射和空气泡洗净技术。首先用不含清洗液的温水进行喷淋粗清洗。然后,用升降机降入槽浸泡。此时,从底部喷出的空气泡与从侧面出来的喷流相结合,即使不加清洗剂,大部分的油污被清洗干净,与单一浸泡清洗方式相比也能获得满意的清洗效果。为进一步的真空清洗打下了基础。由于前室没有加清洗液,油水的分离性好,便于废油的回收。
真空清洗。在前室清洗后,把工件送往真空室,通过真空减压将残存的油和水蒸发。运用真空水蒸汽馏和真空共沸蒸馏原理,解决了以往水类清洗洗净能力差的缺点。
真空干燥。真空清洗后,工件上仅有残存的水,已经没有残油。为防止水对工件的锈蚀,应进行快速干燥。而真空干燥是快速干燥最有效手段。
超声波清洗技术。超声波清洗技术是利用超声波的空化效应、加速度效应、声流效应,能增强液体和工件表面的各种物理作用和化学反应,可降低溶液中化学介质的相对量,或以污染小的弱介质代替污染大的介质,因而超声波技术是一种有应用价值的高效环保表面清洗技术。
超声波清洗原理是超声波清洗机是把每分钟高达几十(20~33)kHz的超声波交变信号,通过换能器(超声波发生器,将电能转换成机械能)转化成上下运动的振动波,并通过清洗机槽底部或侧面,甚至上面作用于清洗液中。在清洗液中产生数以万个微小气泡,这些气泡在超声波不停的作用下,会不断地产生,又不断地闭合。在闭合时,会在液体间相互碰撞而产生上千个大气压力的冲击波,从而破坏不溶性污物,使它们分散于清洗液中。当团体粒子被油污裹着而粘附在清洗件表面时,污油被乳化,固体粒子脱离,从而达到表面净化的目的。
超声波的两个主要参数。频率和频率密度。频率20~33kHz;频率密度=发射功率(W)/发射面积(cm2)。
超声波清洗介质及工艺参数:
清洗介质:超声波清洗介质一般采用化学溶剂和水基清洗剂,液体清洗剂一般由表面活性剂、赘合剂及其他助剂等组成。清洗介质的化学作用可加速超声波清洗效果,超声波清洗是物理作用,两种作用相结合,可达到充分、彻底的清洗。
超声波清洗工艺参数包括功率密度和清洗温度。其中,超声波的功率密度越高,空化效果越强,速度越快,清洗效果越好。(超声波频率:超声波频率越低,在液体中的空化越容易,适合于精细的工件清洗)。一般来说,超声波的清洗温度在30~40℃时的空化效果最好;但温度越高,清洗剂作用越显著。通常超声波清洗时,采用40~60℃的工作温度。
超声波清洗的优点。同其他清洗方式相比,超声波清洗显示了巨大的优越性,尤其在专业化、集团化的生产企业中,已逐渐用超声波清洗取代了传统的的清洗工艺,很容易将带有复杂外形,内腔和细空的零件清洗干净。对一般的除油、防锈等工艺过程,在超声波作用下只需两三分钟即可完成,速度比传统方法提高几倍,甚至几十倍。清洁度也能达到高标准,适合于对产品表面质量和生产效率要求较高的场合。并且超声波清洗节省溶剂、热能、工作场地和人工等。
超声波清洗工艺流程。超声波清洗一般工艺流程为:超声波清洗→超声波漂洗→喷淋漂洗→烘干等工序。
超声波技术是一种高效、环保表面清洗技术。目前应用已相当成熟、广泛,发达国家已超过90%的相关企业采用此项技术。航空发动机零件、汽车及摩托车发动机零件等采用超声波清洗获得良好效果。