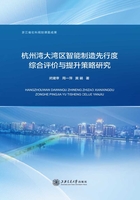
2.2 智能制造的提出
2.2.1 智能制造的定义
1988年,美国学者保罗·肯尼思·莱特(P.K.Wright)和大卫·艾伦·伯恩(D.A.Bourne)在合著的《智能制造》(Manufacturing Intelligence)[9]一书中指出,智能制造是通过集成知识工程、制造软件系统、机器人视觉和机器控制对制造技工的技能和专家知识进行建模,以使智能机器人在没有人工干预的情况下进行小批量生产。1989年,D.A.伯恩组织完成了首台智能加工工作站(intelligent machining workstation, IMW)的样机,被认为是智能制造机器发展史的一个重要里程碑。
1990年4月,日本倡导“智能制造系统(intelligent manufacturing system, IMS)国际合作研究计划”[10],美国、欧盟、加拿大、澳大利亚等发达国家和地区相继参与。该计划将智能制造定义为一种由智能机器和人类专家共同组成的人机一体化智能系统,其在制造过程中能进行智能活动(如分析、推理、判断、构思和决策等),强调通过人与智能机器的合作共事,实现不断扩大、延伸并部分取代人类在制造过程中的脑力劳动。IMS总投资达40亿美元,旨在克服柔性制造系统(fexible manufacture system, FMS)、计算机集成制造系统(computer intergrated manufacturing system, CIMS)的局限性,把日本工厂和车间的专业技术与欧盟的精密工程技术、美国的系统技术充分地结合起来,开发出能使人和智能设备都不受生产操作和国界限制、彼此合作的高技术生产系统。IMS的目标是要全面展望21世纪制造技术的发展趋势,先行开发下一代的制造技术,同时致力于全球制造信息、制造技术的体系化、标准化。1993-1994年,IMS在日本、美国、欧洲、加拿大和澳大利亚等地开展了6个试点项目,73家公司和60多所大学和研究机构参与了项目研究。
20世纪90年代,美国国家科学基金会开始着重资助制造过程中的智能决策、智能协作求解、智能并行设计、智能物流传输等研究内容。1991年,美国提出“先进制造技术(advanced manufacturing technology, AMT)[11]发展战略”。同年,韩国也提出“高级先进技术国家计划”(简称G-7计划)。
进入21世纪,日本、美国、欧洲等地再次掀起智能制造的浪潮,将智能制造视为21世纪全球制造业科技竞争的制高点。
2011年6月,美国智能制造领导力联盟发布《实施21世纪智能制造》报告[12],指出智能制造是先进智能系统强化应用、新产品快速制造、产品需求动态响应,以及工业生产和供应链网络实时优化的制造。其核心技术是网络化传感器、数据互操作性、多尺度动态建模与仿真、智能自动化以及可扩展的多层次网络安全。
2012年3月27日,我国科技部组织编制的《智能制造科技发展“十二五”专项规划》[13]认为:智能制造是面向产品全生命周期,实现泛在感知条件下的信息化制造;智能制造技术是世界制造业未来发展的重要方向之一,是推动我国传统制造产业的结构转型升级的重要途径,全面开展智能制造技术研究将是发展高端装备制造业的核心内容和促进我国从制造大国向制造强国转变的必然。
2013年4月,德国的“工业4.0”将智能制造解释为通过广泛应用互联网技术,实时感知、监控生产过程中产生的海量数据,实现生产系统的智能分析和决策,生产过程变得更加自动化、网络化、智能化,使智能生产、网络协同制造、大规模个性化制造成为生产新业态。该战略规划强调智能制造要完成由集中式控制向分散式增强型控制的基本模式转变,建立一个高度灵活的个性化和数字化的产品与服务的生产模式,建设信息物理系统网络,实现智能工厂和智能生产,完成产品制造的纵向集成、横向集成、端到端集成,并实现生产由集中向分散转变,产品由趋同向个性转变,用户由部分参与向全程参与转变。
2016年2月,美国国家标准与技术研究院工程实验室系统集成部门发布《智能制造系统现行标准体系》[14],明确指出智能制造生态系统要打造互操作性,并增强制造企业生产力的全面数字化,通过设备互联和分布式智能来实现实时控制和小批量柔性生产,构建快速响应市场变化和供应链失调的协同供应链管理,利用集成和优化的决策支撑提升能源和资源使用效率,通过产品全生命周期的高级传感器和数据分析技术实现高速的创新循环。智能制造有别于其他基于技术的数字化制造范式,具备自我完善和生态体系进化能力,是下一代制造的目标愿景。
2016年2月,国家工业和信息化部、财政部联合制定的《智能制造发展规划(2016-2020年)》[15]将智能制造定义为基于新一代信息通信技术与先进制造技术深度融合,贯穿于设计、生产、管理、服务等制造活动的各个环节,具有自感知、自学习、自决策、自执行、自适应等功能的新型生产方式。该规划进一步指出,加快发展智能制造是培育我国经济增长新动能的必由之路,是抢占未来经济和科技发展制高点的战略选择,对于推动我国制造业供给侧结构性改革,打造我国制造业竞争新优势,实现制造强国具有重要战略意义。
表2-4列出了上述各智能制造的定义和侧重点。
表2-4 智能制造的定义及侧重点

本书采用我国《智能制造发展规划(2016-2020年)》给出的智能制造定义,强调前沿信息技术与先进制造技术的深度整合升级,以及制造全过程自主柔性的智能协同。
2.2.2 智能制造的内容与特点
智能制造将互联网技术、设备技术、云计算和大数据等信息化技术应用于生产、控制、操作、制造执行、企业运营、分析决策、商业模式、协同创新等过程,旨在实现自动识别、自动记录、自主分析、自主判断、自主决策、自主优化,并通过设备联网、智能运营模式、协同创新对传统制造业进行升级改造,并实现企业管理过程的智能化、柔性化、集成化。智能制造通过广泛应用互联网技术,实时感知、监控生产过程中产生的海量数据,实现生产系统的智能分析和决策,使生产过程变得更加自动化、网络化、智能化,使智能生产、网络协同制造、大规模个性化制造成为生产新业态。
标准化是智能制造的前提条件。标准为工业大数据提供了一个可持续发展的基础环境,为实现技术创新以达到智能制造要求奠定了坚实的基础,是信息系统、生产制造系统、自动化系统在产品的设计、生产、物流、销售、服务全生命周期中协同互动的保障。产品的智能化、装备的智能化、生产的智能化、管理的智能化以及服务的智能化,要求数据信息能够在装备、人、企业、产品之间实现实时交换、准确识别、智能处理以及快速更新,必须通过制定成体系的技术标准、服务标准、管理标准和安全标准来完成。标准不仅体现了某一国家的技术基础和产业基础,也是国与国之间产业实力的竞争和对国际市场话语权的竞争。积极参与并争取主导制定关键领域的国际标准,是争夺智能制造国际话语权的重要手段。
智能产品是智能制造的主要载体。智能产品是具备一项或多项智能特性的智能装置、智能设备或智能终端,其通常将现代通信技术、传感技术应用于制造业,比如将传感器、存储器、传输器、处理器等设备置入产品当中,从而使产品具有动态存储、通信与分析能力,具有可追溯、可追踪、可定位的特性。智能产品可以划分成三个不同的智能化水平[16]:一是基础智能,即实现产品数据感知、采集、集成、分析,实现设备自诊断、自适应、自决策;二是系统智能,即通过机器学习和数据挖掘,获取并分析用户行为、产品偏好信息,实现产品自学习、自适应,并完成与其他智能产品的信息互联与协同集成;三是交互智能,即通过人工智能和大数据分析,建立智能化人机交互系统,实现产品与用户需求的高效互动及智能匹配,从而形成智能制造的新兴商业模式。
智能制造装备是智能制造的重要内容。智能制造装备需要实现以人为决策核心的人机和谐系统向以机器为主体的自主运行方向转变[16,17]。智能制造装备主要包括先进灵敏的传感器组件、灵活多用的控制系统、工业机器人操纵设备、自动化设备生产线[18]。生产企业在装备智能化转型过程中可以逐步实现单机智能化、单机装备互联、智能生产线、智能车间、智能工厂,并最终将市场和消费者需求互联融入装备升级改造过程,完成全产业链装备智能化。
智能生产是智能制造的主要呈现。智能生产是指将智能技术应用于生产领域的一种新生产模式[19],主要通过构建智能化生产系统、网络化分布生产设施,实现生产过程的智能化。智能生产包含由智能装备、传感器、过程控制、智能物流、制造执行系统、信息物理系统组成的人机一体化系统。智能生产的目的是达到设计、生产、管理的数字化、网络化和智能化,是以智能工厂为核心,将人员、机器、方法、原料、环境连接起来,多维度深度融合,最终实现产业模式转变,是智能制造的必然结果。产业模式的智能转变必然实现从以产品为中心向以用户为中心的转变,由大规模流水线生产向定制化规模生产的转变,由生产性制造向服务型制造的转变[20]。